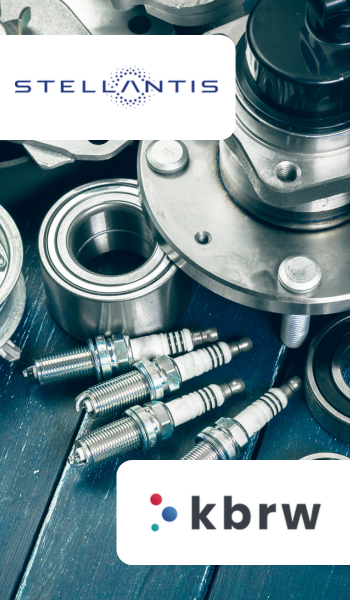
Circular Economy: How Stellantis Optimizes the Recycling and Reuse of Damaged Car Parts
👇Download the case study👇
Reduced processing times for returns
Reduced vehicle downtime and improved customer satisfaction
Parts traceability and quality control support
Guaranteed compliance with internal quality standards and reliability of the deposit system
Reliable deposit system and KPI monitoring
Greater visibility on efficiency and ROI, for Stellantis and its stakeholders
Need

Need: establish end-to-end traceability for the recycling and reuse of used and damaged auto parts
One of the world’s leading car manufacturers, Stellantis consolidated its commitment
to sustainability with the launch of its SUSTAINera initiative in 2019. At the heart of this dynamic, the recycling and reuse of used and defective car parts (or “carcasses”) remain key. A dedicated supply chain makes it possible to sort these carcasses and assess their quality, for them to be reused, reconditioned or recycled.
To accurately track this process, a powerful, 24/7 traceability tool was needed to to improve auditability and establish a continuous improvement process, but also to boost productivity throughout the supply chain and reduce the processing time of parts returns.
Challenges

Challenges: bring together a wide range of players and flows around a unified process, supported by a single tool
Stellantis has a huge number of stakeholders in its circular economy – from garages to sorting centers and hubs, each with its own systems and workflows. The aim was to move from a manual and fragmented process to a consolidated and integrated digital approach, tailored to the different needs of the brands within the Stellantis network. Stellantis needed a tool that integrated perfectly with its IT ecosystem and that of its partners, so it could coordinate the entire reverse logistics chain.
Solution

Solution: a flexible traceability solution tailored to every need, reducing processing times of parts returns
The solution developed by Kbrw quickly proved its worth and meant that procedures for returning parts between different countries, brands and suppliers could now be standardized while including the option of local customization.
Its main strength lies in its ability to perform different actions across many users and different profiles (independent and authorized repairers, local hubs, national hubs, sorting center), while being easy to use. For instance, the sorting center teams benefit from a pre-sorting system, used to manage anomalies that occurred before the sorting center, such as scanning or computer status errors. The solution includes features that help curtail these
anomalies and minimize errors, and also manages logistics and financial flows to allow reimbursements to be triggered via the SAP module used by the Group.
It is now the global logistics platform for tracking carcasses and streamlining flows between garages, hubs and sorting centers.

Need: establish end-to-end traceability for the recycling and reuse of used and damaged auto parts
One of the world’s leading car manufacturers, Stellantis consolidated its commitment
to sustainability with the launch of its SUSTAINera initiative in 2019. At the heart of this dynamic, the recycling and reuse of used and defective car parts (or “carcasses”) remain key. A dedicated supply chain makes it possible to sort these carcasses and assess their quality, for them to be reused, reconditioned or recycled.
To accurately track this process, a powerful, 24/7 traceability tool was needed to to improve auditability and establish a continuous improvement process, but also to boost productivity throughout the supply chain and reduce the processing time of parts returns.

Challenges: bring together a wide range of players and flows around a unified process, supported by a single tool
Stellantis has a huge number of stakeholders in its circular economy – from garages to sorting centers and hubs, each with its own systems and workflows. The aim was to move from a manual and fragmented process to a consolidated and integrated digital approach, tailored to the different needs of the brands within the Stellantis network. Stellantis needed a tool that integrated perfectly with its IT ecosystem and that of its partners, so it could coordinate the entire reverse logistics chain.

Solution: a flexible traceability solution tailored to every need, reducing processing times of parts returns
The solution developed by Kbrw quickly proved its worth and meant that procedures for returning parts between different countries, brands and suppliers could now be standardized while including the option of local customization.
Its main strength lies in its ability to perform different actions across many users and different profiles (independent and authorized repairers, local hubs, national hubs, sorting center), while being easy to use. For instance, the sorting center teams benefit from a pre-sorting system, used to manage anomalies that occurred before the sorting center, such as scanning or computer status errors. The solution includes features that help curtail these
anomalies and minimize errors, and also manages logistics and financial flows to allow reimbursements to be triggered via the SAP module used by the Group.
It is now the global logistics platform for tracking carcasses and streamlining flows between garages, hubs and sorting centers.
Read the whole story: download the case study
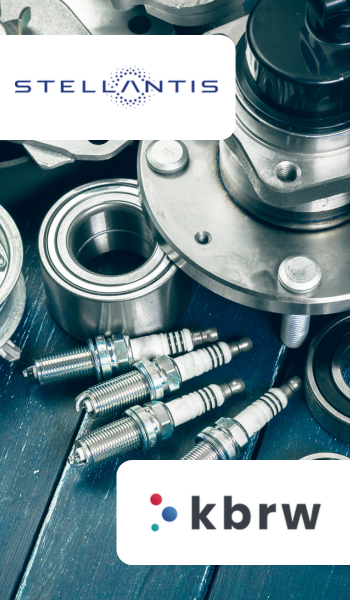